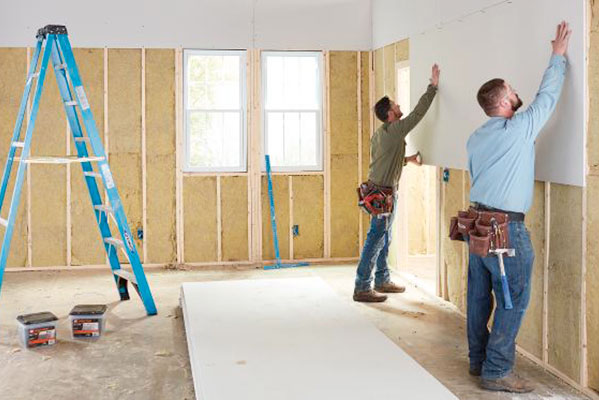
It can be difficult to install resilient channels. This requires extra care, including the incorporation of fire requirements. If installed incorrectly, the resulting STC rating can be disastrous. To prevent this, you must be aware of common mistakes when installing resilient channels.
The most common error that can be made when using the wrong type or resilient channel is to not properly identify it. There are some types that are not compatible and may be incompatible with one another. The wall assembly might compromise the acoustical benefit of the resilient cable. An alternative is to use a resilient channel like the USG RC-1. These channels have long slotted holes that impede the passage of airborne sound vibrations.
Screws that are too small can also be a mistake. Too few screws can penetrate the stud framing. They also nullify the advantages of the resilient channel. At least one-inch should be the length of your screws. A five-eighths gypsumboard would require a screw measuring approximately one-and-a half inches. But, the screw should never fall over the stud. It should instead be installed between the framing elements.
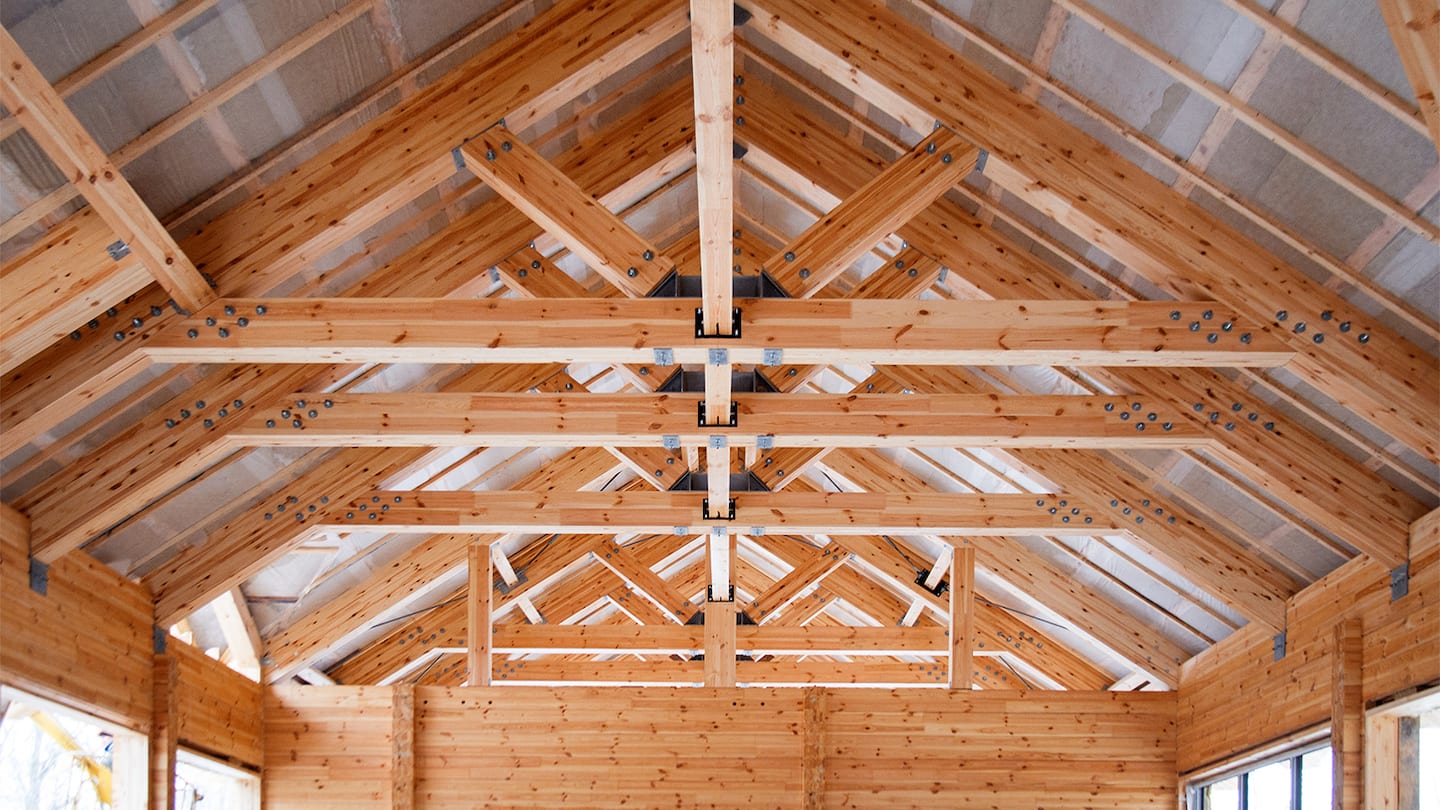
Inadvertently screwing drywall screws into framing can happen in some cases. This can lead to a "short circuit", which can greatly reduce the effectiveness and efficiency of the wall assembly.
Acoustical experts can help you choose the right resilient channel for your project. They will be able to test your wall and decide if the channel you are choosing is the right one. The wrong channel can cause you to lose time and money.
There are many types of resilience channels available. Some are shaped as a furring channel with a hat. Some are cut in a cross-section. All of these are designed to reduce sound-borne noise. They perform differently depending the type of construction used and the place they are placed.
Generally, the most effective resilient channel product is the 25-gauge furring hat channel. The higher gauge material offers extra protection against short-circuiting. You can install smaller products with a lighter gauge, but they will often produce worse results.
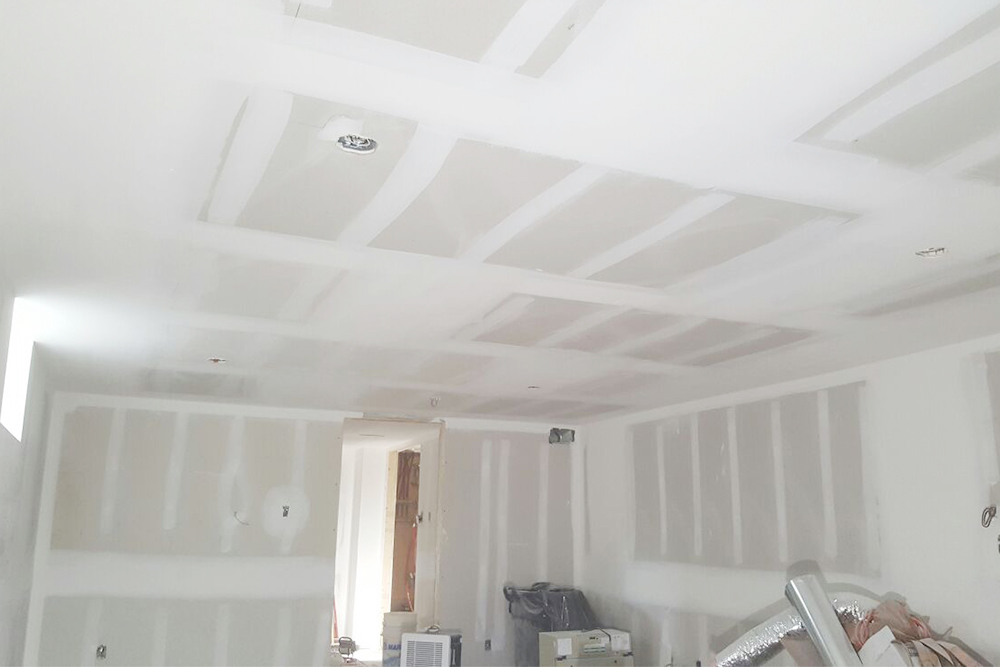
Resilient channel are used to install resilient channels in walls, ceilings, or shear plywood. These resilient channels are used frequently in projects that need additional soundproofing. The resilient channel can be a great option for reducing noise from structures when installed properly.
Resilient channels are not recommended to mount heavy items because they are not connected directly to the studs. They can be attached to either side of the wall, but should be placed on the opposite side of the studs. Although they are simple to install, they do not allow for heavy objects like bookshelves or pot lamps. Similarly, the screws that attach them to the gypsum board should be mounted perpendicular to the studs.
There are several important considerations to be aware of, regardless of the type of resilient channel that you use. The most important thing is to make sure the channel faces are attached to the gypsum boards by using screws at least 1/2 inch long.
FAQ
How long does it take for a home to be renovated?
It all depends on the project's size and how many hours you spend each week. The average homeowner spends between three to six hours per week on the project.
How important do you need to be preapproved for a mortgage loan?
Pre-approval for a mortgage loan is essential. It will give you an estimate of the amount you will need. It can also help you determine your eligibility for a particular loan program.
Is there any way to save money when renovating my home?
It is possible to save money by doing the work yourself. Consider reducing the number or people that you employ during renovations. Another option is to try to lower the cost of the materials you use in your renovations.
Statistics
- It is advisable, however, to have a contingency of 10–20 per cent to allow for the unexpected expenses that can arise when renovating older homes. (realhomes.com)
- On jumbo loans of more than $636,150, you'll be able to borrow up to 80% of the home's completed value. (kiplinger.com)
- Design-builders may ask for a down payment of up to 25% or 33% of the job cost, says the NARI. (kiplinger.com)
- The average fixed rate for a home-equity loan was recently 5.27%, and the average variable rate for a HELOC was 5.49%, according to Bankrate.com. (kiplinger.com)
- A final payment of, say, 5% to 10% will be due when the space is livable and usable (your contract probably will say "substantial completion"). (kiplinger.com)
External Links
How To
How to Renovate an An Old House
Let's start by deciding what type of renovations you would like to undertake. This could range from simple updates to your kitchen appliances, to completely changing the look of the entire house.
Once you've decided what sort of renovation you want to carry out, then you need to think about how much money you have available to spend. You may find that your funds are not sufficient to cover the whole project. If this happens, you might need to make difficult decisions about which areas in your home you can afford to upgrade and which ones to keep the current budget.
Before you start work on your renovations, there are a few things you should consider. The most important thing is to ensure that you get any permits required for the job. You should also check whether you require planning permission for certain types of work. You might have to apply for building permission if you want to add an extension to your home.
Before you start work on the house it is best to check with the local council website to determine if additional permits are required. Also, check whether you need planning permission for each part of the house that you intend to renovate. For major projects like a new roof installation, your insurance provider may need to be contacted to confirm that you have adequate coverage.
The next step after getting all the permits you need is to choose the right tools and materials for the job. There are many options, so take the time to thoroughly research them. Some of the most common items that people use during their renovation projects include paint, wallpaper paste, flooring, tiles, carpets, insulation, fencing, doors, windows, lighting, plumbing, heating systems, electrical wiring, plasterboard, timber, concrete, bricks, tiling, mirrors, sinks, taps, toilets, washing machines, ovens, refrigerators, microwaves, dishwashers, vacuum cleaners, carpet cleaning equipment, air conditioning units, fireplaces, chimneys, and even garden furniture!
You should consider the product's overall quality when shopping for these items. Quality products last longer than cheaper products and are less expensive. When you are buying any item, ensure that you only purchase what is necessary for the job. Don't buy too many because you could end up wasting precious resources and having to discard large quantities of material. Instead, purchase only what you need.
Once you have chosen the materials, it is time to plan where you will store them while you work on the property. You might need storage space if you are renovating large areas of your house. You could also ask your family or friends for help moving the items.